How To Choose The Best Cutting Tools For PCD?
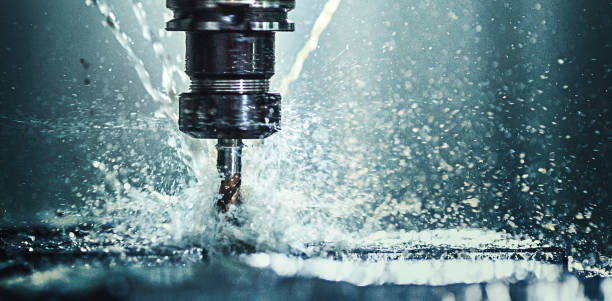
You might be wondering how to choose the best PCD cutting tool. Read on for
the basics of PCD cutting tools, including their characteristics and
applications. You can then begin to prepare your edges. You'll eventually get
the results that you want. These are the top factors to think about when
selecting pcd
reamer cutting speed. It is essential to consider these things because they
can affect your work's performance.
The correct pcd cutter tool
The cost of PCD cutting tools is more expensive than other carbide materials
however they provide greater precision and last longer as compared to carbide
cutters. PCD tools can improve the performance of carbide tools, but they are
not always the most efficient choice. Cost-benefit analysis should be done
within the context of the machine's machining procedure. To avoid errors and
increase productivity, it is important to have a thorough understanding of the
products as well as the process of manufacturing.
PCDs are more versatile than other materials such as carbide. For instance,
aluminum-based products are becoming more popular in the automotive industry and
cutting tools is a common option for these parts. It is not recommended to use
them for ferrous material. To meet your needs TOMMASIN UTENSILI makes custom PCD
tools. These tools are able to cut complex and intricate components.
Specifications
PCD cutting tools offer a variety of advantages. These tools have high
durability with a high level of surface roughness as well as high dimensional
accuracy. Woodworking, non-metallic and ceramic materials are the primary
processing tools. Additionally the pcd tool can process various
fiber reinforced composite materials and a variety of metallic alloys. PCD
cutting tools come in three different types that include piston series cutters
hub cutters and inserts.
To investigate the wear characteristics of PCD tools, we carried out various
tests. We employed two grinding techniques to make a three-dimensional PCD
device and then tested them in high speed titanium alloy cutting. This research
was designed to discover the wear mechanism of PCD tools through analyzing
cutting forces, geometry, and morphology of worn. The results of this research
will help us improve the design of PCD cutting tools.
Applications
A business requires the most effective PCD cutting tools in order to make a
product that is precise and efficient. PCD cutting tools are produced by
rigorous design and engineering processes. They are designed and built with
quality in view. This ensures longer tool lifespan, better throughput and lower
costs for ownership. A good PCD cutter tool will lower the cost of your final
product without sacrificing quality and productivity.
When selecting the right cutting tools for PCD, be sure to take into
consideration the type of material you need to cut. For instance carbide tools
will be worn out quickly and require to be replaced more often. Other
non-ferrous substances like fiberglass and copper require PCD tooling. They also
retain sharper cutting edges over time, making them ideal for various
applications. A PCD insert is an excellent choice if you require a tool to
endure extreme temperatures.
Edge preparation
It is vital to comprehend the importance of edge preparation prior to
deciding on PCD cutting tools. Edge preparation is essential for efficient
manufacturing and allows cutting tools to operate at their best. Edge
preparation is quickly becoming a mandatory feature for every pcd reamer cutting
speed. But how do you determine what tools are best suited to your needs? Read
on for helpful tips! Let's start by defining what edge preparation is.
Carbide drills aren't easy to prep. It can involve t-land and grinding. PCD is a fan of edge preps and organized hones. They can be costly and vary in size depending on the type of tool. PCD is generally used "up sharp." This depends on the supplier. Some suppliers run PCD instruments 10,000 times before being considered to be no-sharp.
Comments
Post a Comment